Published 08:48 IST, March 24th 2023
NASA's redundant high-tech substance finds its way to jeans, sportswear
Formerly intended for space, NASA's high-tech substance somehow seeped its way into the commercial realm, specifically into the world of jeans and sportswear.
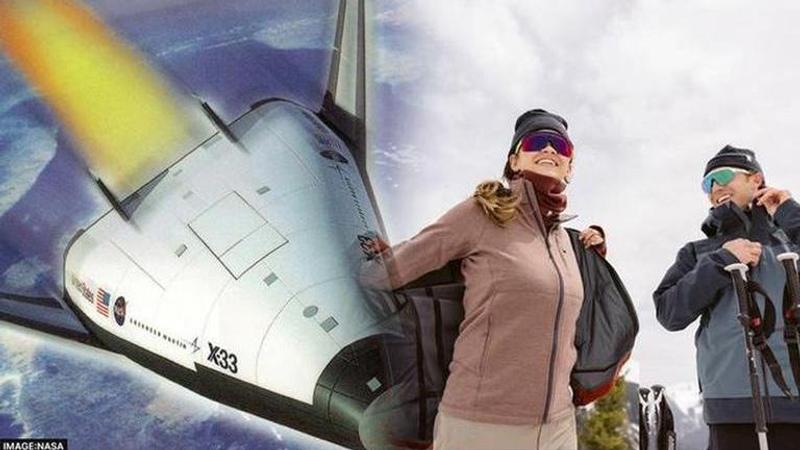
In the 1990s, a high-tech substance dubbed Protective Coating for Ceramic Materials, or PCCM, was used by NASA for the Reusable Launch Vehicle programme meant for helping hypersonic spaceplanes go on repeated space missions. Today, the material is no longer in use by the space agency, but it continues to change the world of clothing, especially jeans, sports attire, and outerwear.
About 20 years after the programme was abandoned, a substance known as Protective Coating for Ceramic Materials (PCCM), came into being in the private sector, completely transforming the world of clothing. PCCM was developed by NASA’s Ames Research Center in Silicon Valley, California, in order to safeguard the heat shields of spaceplanes during re-entry in the atmosphere.
The agency patented the coating, and later on Emisshield Inc. (formerly known as Wessex Inc.) licensed the material to be used in commercial everyday items. But PCCM isn't your regular insulator. It possesses impressive emissivity, which is the ability to absorb heat from a heat shield and emit it away from the spaceplane.
In 2013, the unique substance caught the eye of Brad Poorman and Jim Hind, who founded Clean Textile Technology LLC. According to NASA's official website, the duo reached out to Emisshield, which decided to license the material to Clean Textile Technology LLC exclusively in return for a share.
NASA's high-tech substance births Trizar
By the year 2015, the material and fabric amalgamated to create Trizar, which quickly shot to fame and yielded some 300,000 jackets made out of the material that year. Since then, the company has ventured into production of jeans, sportswear, and face masks and put PCCM to good use.
“During the pandemic, Emisshield was awarded patents around the fibers and fabrics we had developed, and we did a lot of R&D while the factories were shut down,” Poorman said about how the company navigated the COVID-19 pandemic. Poorman also revealed that initially, the material was printed onto fabrics, but with enough hard work, the company was able to add it to thread or yarn, making the process a whole lot easier and feasible. “By getting it into the yarn, we’ve been able to deliver performance without adding any weight and with much less cost,” he said.
Updated 08:48 IST, March 24th 2023